Address: Unit 19, 54 Fairey Rd, South Windsor NSW 2756
Workplace Electrical Hazards: How to Keep Your Employees Safe
Electricity is everywhere: silent, invisible, and powerful. It does many important things for society: lighting up offices, keeping machines running, powering essential equipment, and fueling productivity. It’s a force that drives modern workplaces forward. But when mishandled, it can turn from an everyday convenience into a serious threat.
A faulty wire. An overloaded circuit. A tool with worn insulation. Even the smallest lapse in maintenance or safety can lead to electric shocks, burns, fires, or worse. Yet, most electrical hazards are entirely preventable with the right awareness and precautions.
In this guide, we break down the most common workplace electrical risks, their causes, and the practical steps every business can take to keep employees safe.
What is the Meaning of Electrical Hazard?
An electrical hazard is any condition that exposes individuals to the risk of electric shock, burns, fires, explosions, or other injuries caused by electrical energy. These hazards can arise from direct or indirect contact with electricity, including faulty wiring, damaged electrical equipment, exposed live conductors, and improper grounding.
Electrical hazards can be categorised into different types, including:
- Shock Hazards – Occur when a person comes into contact with an electrical source, causing electric current to pass through the body.
- Arc Flash Hazards – Result from high-energy discharges that produce intense heat, light, and pressure waves, capable of causing severe burns and explosions.
- Fire Hazards – Happen due to overheated wires, overloaded circuits, or faulty electrical components, potentially leading to workplace fires.
- Explosion Hazards – Can occur when faulty electrical equipment ignites flammable gases, vapours, or dust in hazardous environments.
Understanding these hazards is critical for implementing effective safety measures and ensuring compliance with workplace regulations. Electrical hazards are not only a threat to employee safety but also a leading cause of property damage and business disruptions. Employers must take proactive steps to identify and control these risks before they lead to serious incidents.
For further insights into electrical safety in the workplace, refer to Safe Work Australia’s Electrical Safety Guidelines.
Understanding Workplace Electrical Hazards
Electrical hazards are a major concern in any workplace, as they can lead to severe injuries, fires, or even fatal incidents. While all industries rely on electricity, the risks vary depending on the type of work environment, the electrical infrastructure in place, and the safety measures followed.
Some workplaces have a higher likelihood of electrical incidents due to the nature of their operations. For example, construction sites, manufacturing plants, and industrial facilities often involve high-powered machinery, temporary wiring, and exposure to harsh conditions that can increase the chances of electrical failures
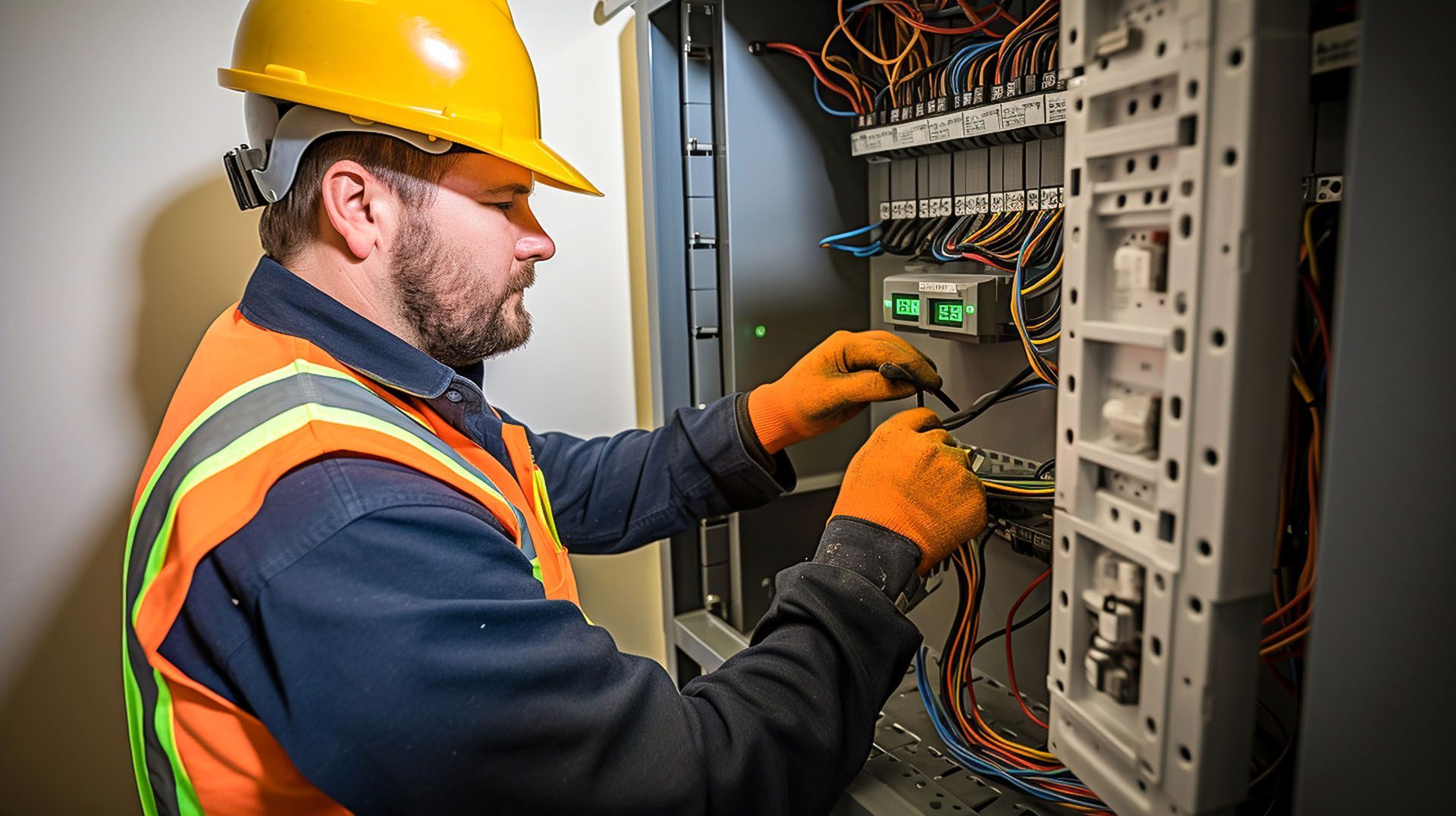
Industries Most Affected by Electrical Hazards
Electrical hazards exist in virtually every industry. Although construction faces the highest risk due to live power lines, power tools, and high-voltage electrical equipment, other sectors also deal with serious electrical dangers that can lead to workplace injuries, equipment damage, and operational disruptions.
Construction & Industrial Worksites
Workers in construction, manufacturing, and industrial sectors regularly interact with high-powered machinery, temporary wiring, and exposed electrical systems. Common hazards include:
- Overhead power lines – Contact can result in fatal electrocution, especially when using scaffolding, ladders, or heavy equipment.
- Faulty tools and damaged wiring – Frayed cords and worn-out power tools or electrical equipment pose a high risk of electric shock.
- Overloaded circuits and improper wiring – Exceeding the electrical capacity of a system can lead to overheating and fires.
Offices & Commercial Buildings
Even in office environments where electricity use seems low-risk, poor electrical management can create hidden dangers. Some common hazards include:
- Improper use of power strips and extension cords – Overloaded outlets increase fire risks.
- Aging or poorly maintained electrical panels – Faulty breakers and outdated wiring systems can overheat and cause electrical failures.
- Inadequate emergency lighting systems – A power outage or circuit failure can leave employees vulnerable if safety lighting is not properly maintained.
Warehouses & Logistics Centers
Warehouses and distribution centers rely on high-powered lighting, conveyor belts, and charging stations for forklifts and other equipment. Electrical hazards in these environments include:
- Faulty or exposed wiring near storage areas – Damaged cables can pose fire and electrocution risks.
- Wet or high-humidity environments – Water leaks or condensation near electrical systems increase the chance of short circuits and shocks.
- Overloaded charging stations – Multiple machines charging at once can exceed electrical capacity, leading to overheating.
Retail & Hospitality
Retail stores, restaurants, and hotels use a vast range of electrical equipment and appliances, from commercial ovens to POS systems. Electrical risks in these sectors include:
- Faulty kitchen equipment – Overloaded circuits, damaged cords, and improper grounding in restaurant kitchens can lead to electrical fires.
- Extension cord misuse in display areas – Temporary lighting and displays may use daisy-chained extension cords, increasing the risk of overheating.
- Water exposure risks in hospitality – Spilled drinks, cleaning equipment, or faulty pool lighting can create electrical hazards.
Healthcare & Aged Care Facilities
Hospitals, clinics, and aged care facilities rely on critical electrical systems for life-saving equipment, patient monitoring, and emergency backup power. Risks in these settings include:
- Unstable power supply to medical equipment – Poor wiring or overloaded circuits can disrupt essential devices like ventilators and imaging machines.
- Electrical hazards in wet environments – Operating rooms, bathrooms, and patient areas with medical equipment require strict electrical safety protocols.
- Failure of emergency backup systems – Inadequate maintenance of backup generators and RCDs (Residual Current Devices) can put patient safety at risk during a power failure.
Why Workplace Electrical Safety Matters
Electrical hazards aren’t just a safety concern — they’re a business risk. A single faulty connection or overloaded circuit can trigger an electrical fire, bringing operations to a standstill. A serious workplace injury can lead to legal and financial consequences that last for years.
But most electrical incidents aren’t random. They’re actually preventable. Regular inspections, proper training, and compliance with safety regulations don’t just reduce risks; they protect employees, productivity, and electrical equipment. A well-maintained electrical system isn’t just about following the rules — it’s about keeping your workplace running smoothly and safely.
Common Causes of Electrical Hazards
Many electrical hazards can be prevented by identifying and addressing their root causes. Here are some of the most common factors contributing to electrical accidents in the workplace:
1. Insufficient Insulation
Over time, insulation around electrical wiring can deteriorate due to wear, moisture exposure, or even rodent damage. In some cases, improper electrical installation can also result in inadequate or poorly fitted insulation, leaving wires vulnerable to damage. When insulation breaks down, wires become exposed, increasing the risk of shocks, short circuits, and fires.
2. Circuit Breaker Failures
Circuit breakers are designed to trip when an electrical overload occurs. If a circuit breaker malfunctions or is faulty, it fails to prevent overheating, leading to fires and other electrical failures.
3. Damaged Electrical Appliances and Tools
Frayed cords, loose connections, and cracked insulation in electrical tools can result in electrical equipment malfunctions and shocks. Using damaged equipment significantly increases the risk of injury.
4. Improper Use of Extension Cords
Overloading extension cords or daisy chaining (connecting multiple extension cords) can lead to overheating and electrical fires. Businesses should ensure that power strips and extension cords are used appropriately.
5. Lack of Regular Maintenance
Neglecting routine inspections and maintenance increases the likelihood of electrical hazards. Warning signs such as burning smells, flickering lights, or unusual noises should never be ignored.
Regular electrical maintenance helps prevent these hazards by keeping wiring, circuit breakers, and electrical equipment in safe working condition. Routine inspections and timely repairs reduce the risk of electrical failures and keep workplaces safer for everyone.
What Are the Electrical Hazards in the Workplace?
Both employers and employees have the responsibility of staying vigilant in recognising electrical risks. The following are some of the most main electrical hazards encountered in workplaces:
1. Overhead Power Lines
Overhead power lines carry high-voltage electricity, which can cause severe burns or electrocution upon contact. Workers should maintain a minimum clearance of 10 feet and use safety barriers and warning signs near power lines.
2. Damaged Tools and Equipment
Faulty portable electrical equipment and appliances pose a serious risk of electric shock, short circuits, and fires. Frayed cords, loose connections, and cracked insulation should never be ignored. All electrical tools must be inspected before use, and only licensed electricians should handle repairs.
3. Inadequate Wiring and Overloaded Circuits
Incorrectly sized wires can overheat, leading to electrical fires. Ensuring proper wire selection and conducting regular fire risk assessments can help mitigate this hazard.
4. Exposed Electrical Parts
Temporary lighting, open power distribution units, and unprotected insulation can cause electric shocks. Faulty or incomplete electrical installation can also leave wiring and components exposed, increasing the risk of contact with live electricity. All exposed electrical components should be securely covered or repaired immediately to prevent workplace injuries.
5. Improper Grounding
Grounding electrical equipment reduces the risk of electrocution. One of the most common electrical violations is the removal of metallic ground pins—a crucial safety feature that prevents dangerous voltage buildup.
6. Wet Conditions
Operating electrical equipment in wet environments significantly increases the risk of electrocution. Electrical devices that have been exposed to moisture should be inspected and tested by a qualified electrician before use.
Preventing Electrical Hazards in the Workplace
Taking proactive steps to address electrical hazards can help create a safer work environment. Here are essential measures that businesses should implement:
1. Conduct Regular Electrical Inspections
Routine inspections can detect faulty wiring, damaged cords, and malfunctioning electrical equipment. Qualified electricians should conduct these inspections to ensure compliance with safety standards.
2. Provide Proper Training
All employees should receive training on electrical safety, including hazard recognition and emergency response procedures. Workers should be encouraged to report any electrical issues immediately.
3. Implement Lock Out Tag Out (LOTO) Procedures
LOTO procedures prevent accidental re-energisation of electrical systems during maintenance or repairs. Only authorised personnel should have access to locked-out equipment.
4. Install Residual Current Devices (RCDs)
RCDs, also known as safety switches, provide an extra layer of protection by automatically cutting power when they detect electrical faults. RCDs should be tested regularly by electricians offering RCD testing to ensure functionality.
5. Use Protective Equipment
Employees working with electrical systems should wear appropriate Personal Protective Equipment (PPE), including insulated gloves, safety goggles, and flame-resistant clothing.
6. Avoid Overloading Outlets and Circuits
Businesses should ensure that power outlets are not overloaded and that circuits are protected by appropriately rated fuses and breakers. Using suitable electrical equipment helps prevent overheating, fires, and system failures.
7. Encourage Safe Work Practices
Workers should follow best practices, such as:
- Keeping electrical cords and leads off the ground
- Using cable protection ramps
- Avoiding makeshift repairs with electrical tape
- Using battery-powered tools where possible
Legal Responsibilities for Electrical Safety
Employers have a legal duty to manage electrical risks in the workplace under the Work Health and Safety Regulation 2017 (WHS Regulation). Their key responsibilities include:
- Providing safe electrical equipment – Only approved and well-maintained electrical tools should be used.
- Routine maintenance and testing – Electrical systems should be inspected based on workplace conditions.
- Hiring qualified electricians – Electrical work should only be carried out by licensed or registered electricians. Ronika’s Western Sydney commercial electricians are licensed and experienced.
- Ensuring safe work environments – Workers should not operate electrical equipment in wet or hazardous conditions.
For high-risk industries like construction and manufacturing, additional safety regulations apply. Hostile operating environments (e.g., outdoor sites, wet areas) require more frequent inspections and testing.
Electrical Safety Measures for Shared Workspaces
Many workplaces share electrical infrastructure with multiple businesses. In these environments:
- All businesses (PCBUs) must work together to ensure compliance with safety standards.
- Unsafe electrical equipment must be immediately disconnected and only restored after professional testing.
- Emergency procedures should be well-documented and communicated to all workers.
Testing and Maintenance of Electrical Equipment
Regular inspection and testing of portable electrical equipment help identify potential risks before they cause harm. One of the most effective ways to do this is through regular test and tag procedures, which help identify unsafe equipment before it becomes a hazard. Through the routine inspection and labelling of electrical appliances, businesses can prevent failures, maintain compliance, and keep workplaces safe.
To minimise risks, businesses should follow these key recommendations:
- Portable electrical tools should be visually inspected before use.
- Hostile environments (e.g., wet or dusty workplaces) require annual or bi-annual electrical equipment testing to prevent deterioration.
- Construction sites should test electrical tools every three months due to harsh conditions and frequent equipment movement.
- Records of electrical testing must include dates, results, and follow-up actions to ensure compliance and workplace safety.
Final Thoughts
Workplace electrical hazards don’t give warnings. A single overlooked fault — a worn cable, an overloaded circuit, or a neglected switchboard — can escalate into costly downtime, damaged electrical equipment, or even serious injury. But these risks are avoidable with proactive electrical maintenance with a strong focus on identifying electrical hazards before they become a threat.
At Ronika, we offer comprehensive electrical maintenance services to keep your workplace compliant, efficient, and safe. Our team follows AS1851-2012 and the Building Code of Australia, so your electrical systems meet the highest safety standards. Whether you need routine inspections, preventative maintenance, or urgent repairs, we can create a bespoke maintenance package that perfectly fits your business needs.
Stay ahead of electrical risks and partner with Ronika for a safer, more reliable workplace. Contact us today to discuss your maintenance plan.
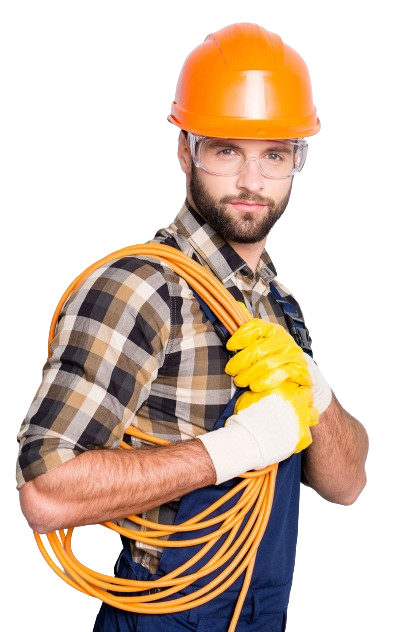